If you browse through IT-related news or visit technology blogs all over the Internet, you might have come to realize that Artificial Intelligence (or simply AI) is omnipresent. It is used in numerous fields and industries, including finance, healthcare, education, transportation, and more. AI may even shed some light on how humans process abstract learning or mimic rapid insect flight.
Although the possibilities of AI seem larger than life, the whole world is still debating the consequences of using AI and the role it is going to play in reshaping our world. Some professionals are sceptical, and the others are welcoming this new reality with arms wide-open.
Despite quite a volume of futuristic imagery such as human-like robots and self-regulating cities, there’s nothing magical about AI. At its core, Artificial Intelligence is just programs (or group of programs). This conclusion poses a reasonable question: how exactly AI will change the industries? For instance, what about the manufacturing domain, the one that has been traditional in its approach for ages? Let’s find out.
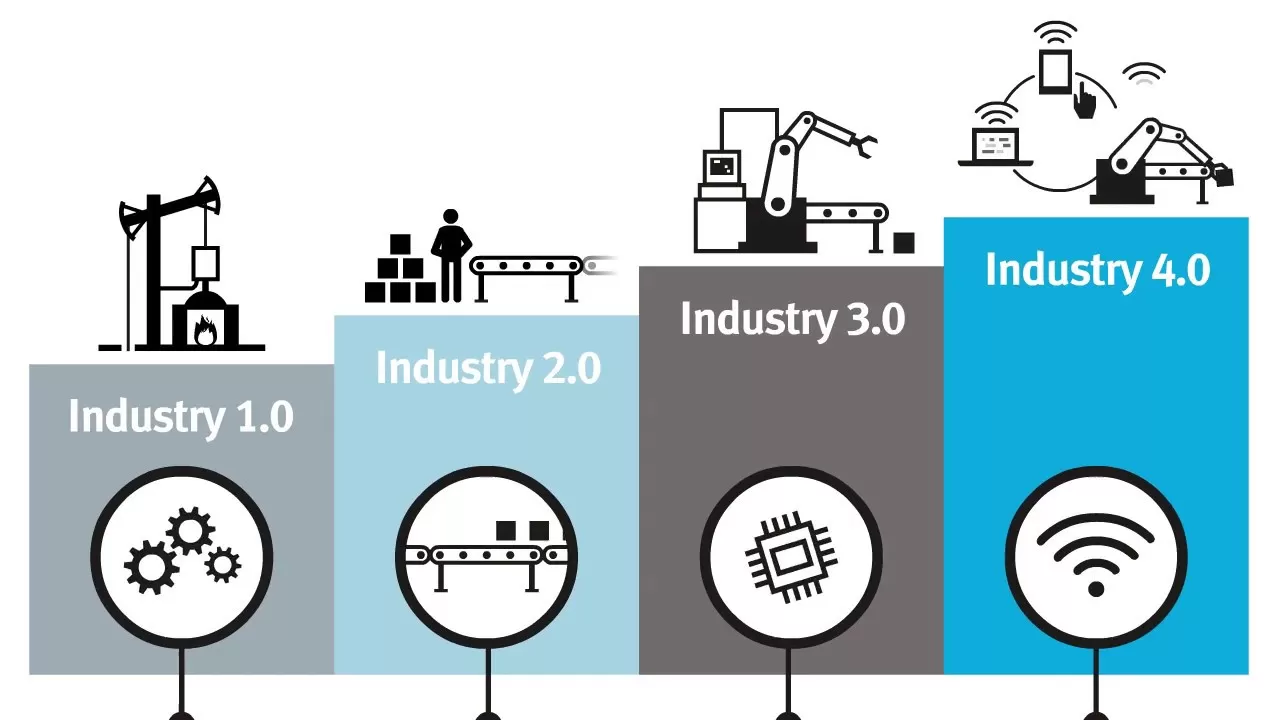
Foremost, it would be fair to say that the term “revolution” which stays in close connection with Industry 4.0 is a bit misleading. Revolutions drastically change the way of things, and if we talk about Industry 4.0 it is more about “evolution” as the domain has to go a long way before any revolutionary changes will really take place. I mean that the creation of a digital environment takes a lot of efforts including instrumentation, connectivity, data collection at the facilities, etc.
Although there’s no problem with connectivity – after all, we’re in 2018 – the use of data seems to be a much harder challenge. And that’s precisely why the notion of “revolution” is way too early to discuss now. Data is the crucial element of Industry 4.0 realm, and AI is the technology to enable this change. Manufacturers should start by dealing with their own operations, planning them in terms of design, development and output at different operational levels.
There’s nothing magical about AI so it shouldn’t be considered as a magic wand for everyone around. First, one has to identify issues in his own operations and then look at whether there’s a technology that can offer a solution. After all, each organization has its own strategy. Quite a considerable number of these companies do not follow industry trends at all. If we talk about digitization, we should start by thinking about the strategy. Again, just creating connectivity can’t produce anything of value on its own.
Another challenge is in the readiness to share data. If manufacturers want to adopt AI, they should also share their data with a third-party. Not every company is ready for that kind of a shift in thinking. Manufacturers have their own established internal processes so their mindset has a distinctive old-school touch if we talk about adopting new technologies. The skills gap is also a big concern in the manufacturing sector. By the year 2025, up to 3.5 million new jobs will available in manufacturing, but the industry is predicted to be short on qualified workers by 2 million or more. People are afraid that AI might take their jobs, but it’s exactly the opposite. Think Uber if you need a good example.
AI could have a similar impact on manufacturing: it will create new jobs and new opportunities. In fact, it’s going to introduce a new class of labor, which will liberate workers from tedious tasks. They won’t have to stare at their screens all day, instead, they will be delegated with higher functions and responsibilities. Manufacturing institutions have to encourage their workers to adopt new skills so they can painlessly drift from front-line roles to managerial ones.
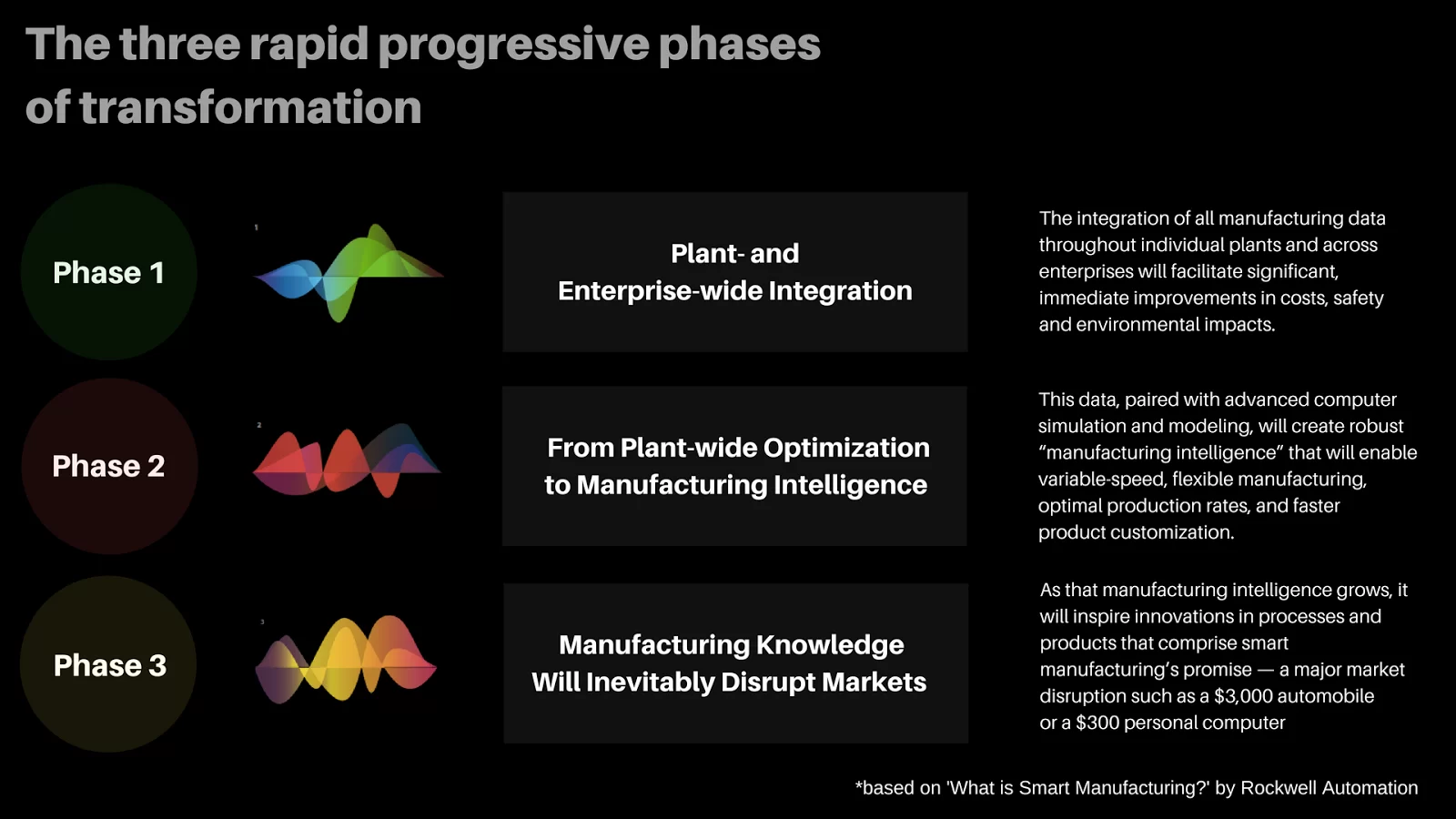
And we don’t have to wait for ages to see the new working paradigm taking its place. For instance, American multinational automaker Ford introduced a project which could be an excellent example of a humans-robots cooperation in assembly lines worldwide. In Cologne, Germany, Ford has introduced new collaborative robots, also known as co-bots, helping workers fit shock absorbers to Fiesta cars at the assembly plant.
The process involves both robots and human workers addressing their tasks together to ensure that the work is done properly. “If we deem that is efficient enough, we can take a look at including them in other plants,” commented Ford representative Karl Henkel. “The co-bots are an ‘and’ proposition and not a ‘or’ proposition. It’s not ‘can this robot do what a worker cannot do?’ They’re complementary, working together as a team.”
Team spirit and cooperation are slowly but gradually forming the perspective that manufacturers need to adopt to start looking at smart factories the right way. It’s not about blindly following trends or do something because your competitors do, it’s about creating jobs for the future. And it’s not about solely the automation process – it’s more about creating new jobs for those processes as long as they go together with automation.
Just like in other industries, artificial intelligence solves the problem of future growth and success in manufacturing. A Forbes Insights survey on AI states that 44% of respondents from the automotive and manufacturing domains label AI as “highly important” to the manufacturing function in the next five years. Another half—49%—said it was “absolutely critical to success.”
So let’s repeat: the road towards digitalization begins with the building of an appropriate strategy. By developing a digital strategy first, you’ll know how and when you can apply AI to your enterprise. Artificial intelligence is not a solution, it just holds the most suitable key to the solution itself. Manufacturers should ask themselves: “Where do we want (and have the opportunity) to automate? Do we already have digitization? If yes, in what measure?”
Sure enough, we’re just witnessing the early stages of AI in manufacturing. But quite often the first step is the most important. Just remember the previous impact of innovations on businesses – for instance, the invention of electricity transformed every business domain. Early stages or not, both deep learning and AI have the potential to transform every industry. Just take a closer look at your business and study current business cases – it’s solely up to you to make a very first move.