The concept of the Internet of Things provided the industrial world with a lot of new opportunities, including organized and continuous data collection from sensors and other devices at facilities. As of today, organizations can collect massive amounts of data on business processes in real time. Besides, thanks to cloud computing, the storage and processing of data don’t come as a tedious challenge anymore. The arrays of historical data go through a sort of a funnel, so to speak, allowing manufacturers to analyze past mistakes and predict future events based on those new insights.
Courtesy of those forecasts, companies have the opportunity to increase their business efficiency by tens of percent. According to Zion Market Research, the market for forecasting analytics is expected to reach whopping USD 10.95 billion by 2022, growing at a CAGR of nearly 21% between 2016 and 2022. The global market for predictive analysis systems will grow by an average of 17.8% annually. As many business practices show, companies that continue to invest in technology and innovation have stronger chances to survive in challenging economic periods. And predictive analytics is undoubtedly one of those innovations not to neglect.
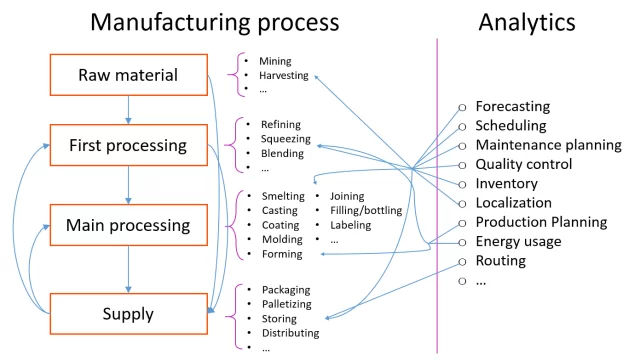
What is predictive analytics anyway? This technique is a set of statistical analysis methods that are developed to extract new information from current and historical data. This information serves as a basis for predicting business processes, trends and behaviors so that a company knows in advance about future events and can adjust its business strategy based on this knowledge. As they say “Knowledge is power”, or, as Eric Siegel specifies in his book “Predictive Analytics: The Power to Predict Who Will Click, Buy, Lie, or Die”: “As data piles up, we have ourselves a genuine gold rush. But data isn’t the gold. I repeat, data in its raw form is boring crud. The gold is what’s discovered therein.”
The basis of predictive analytics is defined by the automatic search for links, anomalies, and patterns between various factors. A large set of statistical modelling methods, data mining, machine learning, neural networks and other mechanisms are used to form a predictive model. Predictive analysis systems allow organizations to reduce risks, optimize resources and improve company efficiency through the adoption of effective management decisions. Predictive analysis is indispensable when a company needs to detect non-obvious patterns, segment goods or customers for marketing purposes, build a sales forecast or change customer base.
Sure enough, predictive analysis has been around for years. However, it required much more information resources and computing power. Back then, only large enterprises and banks could use prognostic analytics tools. They stored the data on the servers, and the processing and analysis of data involved mathematics-statistics or analytics. Nowadays, the servers are being gradually replaced by cloud storage. Artificial intelligence began to perform calculations many times faster than people. The automation of production, emergence of more complex information systems, accumulation of data, and many other factors contributed to the democratization of the predictive analysis domain.
Predictive Analytics in Manufacturing
Predictive analytics represents particular importance for industrial enterprises as their need for processing and understanding of a huge amount of data is unquestionable, and there are high risks of failure when making a decision. As a matter of fact, the data which describes the flow of the process is not always used efficiently while it can be processed to optimize operating processes and improve the technical and economic indicators of a manufacturing facility.
Despite this (sometimes) sad situation, tasks on optimization can be performed at any type of manufacturing facility if there’s a serious level of automation, organized data collection and long-term storage of information. The process follows the following routine: intelligent systems analyze the state of the technological process in real time, predict the further course of the process, determine the level of optimality and, if necessary, change the control parameters or advise the dispatcher. To solve these problems, a predictive mathematical model of the technological process is created using machine learning tools. It analyzes the input parameters, provides a forecast on the process in real time, and suggests its optimization measures. This model is combined with the enterprise control system, MES and ERP systems.
Another task for predictive algorithms is equipment maintenance and repair. Basically, enterprises use basic control mechanisms provided by equipment manufacturers. But the potential of these funds is limited because they do not allow to analyze additional factors affecting the state of the equipment, so one can’t predict the critical situation in advance. Thus, the maintenance department receives a lot of data, but they don’t know how these flows of data are related one with each other.
As a result, a factory’s managers will deal with repair services representatives only following the equipment failure, which leads to downtime, and, consequently, additional costs. By means of machine learning and artificial intelligence, analytics within an enterprise can conduct a continuous research of big data to temporarily address potential equipment failure scenarios. As a result, maintenance time and work are optimized, and the management personnel receives insights on the causes which led to the downtime.
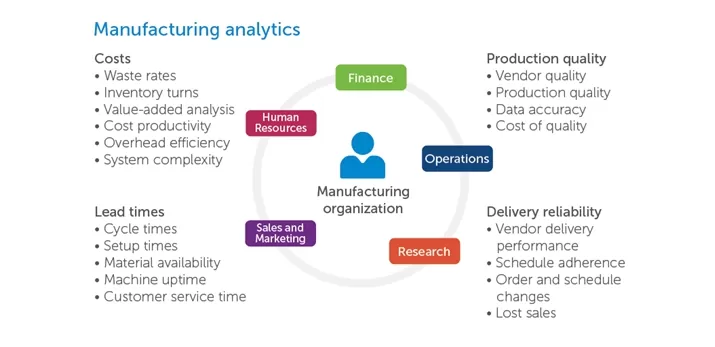
Modern IoT and Big Data capabilities, along with advanced predictive analytics, are becoming an effective tool to reduce costs, improve product quality and increase enterprise productivity. Predictive analytics opens up broad prospects for the further development of companies. In addition to manufacturing industry, forecast platforms are successfully used in banking, insurance, retail, logistics, marketing and many other areas. For example, banks and other financial institutions resort to analytics tools to predict their customers’ behavior. Based on their historical behavior in conjunction with external factors, mathematical algorithms can make profitable personal offers, anticipate sales increase, customer churn, etc. In marketing, mathematical modelling allows you to segment customers according to certain criteria, predict their future behavior (indicate customer value, calculate the probability of a repeat purchase, etc.) and highlight services and products that may be interesting to customers. Predictive models accurately determine effective channels of interaction with the target audience.
Final Thoughts
When embarking on the introduction of a predictive analytics system, it is necessary to bear in mind that the operation of such a system is impossible without a large amount of historical data and the continuous collection of current data. The less data is involved, the less accurate the predictions will be. When adopting predictive analysis tools, companies often face the problem of lack of data, which becomes an insurmountable barrier to forecasting. However, this is the topic for another article.